IN SHORT
How Cognite Data Fusion supports manufacturing plant maintenance workers
Yokogawa used DataOps provided by Cognite, including Cognite Data Fusion (CDF) and InField, to put liberated, contextualized data into the hands of maintenance workers. This allowed them to unlock data in under two days and create a 3D model of assets within 30 minutes. The solution: Improved off-site planning and support, reduced time spent searching for equipment, and enabled workers to conduct maintenance work more efficiently.
CHALLENGE
Yokogawa's data was trapped in complex, siloed systems.
Large-scale digitalization of the manufacturing industry will only be possible if companies make all the data they collect available in a way that’s intuitive to human users and machines.
However, for many manufacturing companies, data is trapped in complex, siloed systems. This makes it more complicated for workers to use the data in their day-to-day activities.
Data scientists must build point-to-point integrations every time they want to develop a new application, and maintenance workers have to access multiple systems to find the information they need.
SOLUTION
Cognite Data Fusion (CDF) unlocked data in under 2 days and created a 3D model of assets within 30 minutes.
In less than two days, Cognite liberated data from Yokogawa’s source systems, including time series, equipment information, historical events, and instruction manuals, collecting it all as a comprehensive set in Cognite Data Fusion (CDF).
Yokogawa and Cognite then identified two specific ways of getting the liberated, contextualized data into the hands of maintenance workers.
The first is InField, Cognite’s flagship application for digital field workers. Available on computers and handheld devices, InField streams data from CDF. By scanning a tag on any piece of equipment in the manufacturing plant, Yokogawa’s maintenance workers can now pull up all real-time and historical data, documentation, maintenance records, pictures, and more information relevant to that equipment.
The second is a digital twin that combines the liberated, contextualized data with a 3D model. After taking about 400 pictures of the Kofu plant, Cognite used photogrammetry to make a 3D model of it in about 30 minutes. Cognite then overlaid the 3D model with real-time and historical sensor data, giving users a powerful visualization tool to explore the plant.
Contextualized data can also enable easier creation and deployment of analytics models powered by artificial intelligence and machine learning. Historically, fault finding, analysis, and diagnosis is done based on data from standalone systems. This means that it is not possible to correlate various signals and systems across a plant. With large amounts of historical data about pump flow, vibration, and events, however, companies can detect anomalies and fault conditions that were previously not possible to diagnose.
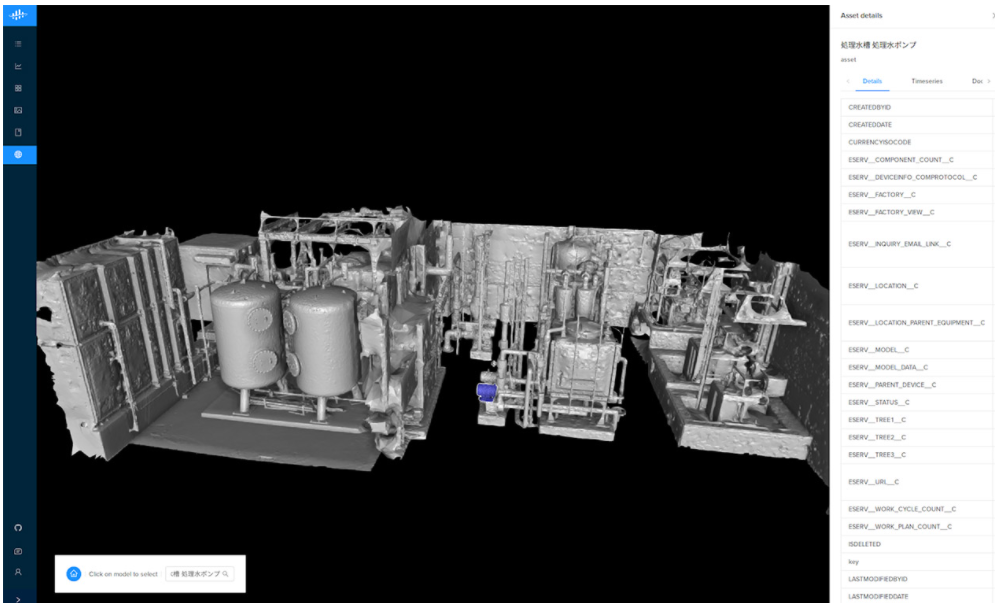
IMPACT
InField enables field workers to collaborate with remote experts looking at the same data. Working together, they can more quickly diagnose errors and conduct maintenance work more efficiently.
The 3D model with contextualized data enables field workers to more efficiently search for and locate equipment and plan remote operations, and also improves off-site planning and support.